Microfluidizer® Technology
In recent years, a diverse spectrum of industry sectors have embraced Microfluidizer® technology for the creation of products with qualities that are only possible using nano-scale materials. Examples include nanoparticles, nanoemulsions and nanoencapsulation.
Advantages of this technology are numerous, and include everything from improving stability, to optimizing material characteristics, to enhanced delivery of hydrophobic drugs to their intended targets.
Unrivaled standards in uniform nanoemulsions, cell disruption and particle size reduction
It’s no wonder that process engineers in industries as distinct as pharmaceuticals, vaccines, fine chemicals, biotechnology, cosmetics, food processing and energy have discovered that Microfluidics represents superior technology for the efficient creation of nanoparticles and nanoemulsions, among other applications.
Although conventional homogenizers can be used to achieve some of these applications, Microfluidizer® processors offer superior results in terms of greater particle size reductions, tighter particle size distributions, repeatability and seamless scalability.
Microfluidizer® technology ensures fluid pressure is converted to high shear forces more efficiently and consistently than is readily achievable using competing technologies. By maintaining constant pressure, Microfluidizer® processors ensure that 100 percent of a given material receives exactly the same treatment.
Inherent differences in Microfluidizer® technology versus high-pressure valve homogenization technology mean far less process energy is converted to heat. This not only saves energy, but also helps prevent thermal effects from altering the physiochemical characteristics of any delicate materials undergoing processing.
How's It Work?
The combination of the constant pressure pumping system and exclusive fixed-geometry Interaction Chamber™ is what makes our Microfluidizer® Technology superior and enables our customers to achieve unparalleled success.
This technology is also instrumental in the production of time-release products, such as drugs, cosmetics, nutraceuticals and even pesticides/herbicides.
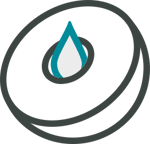
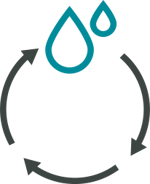
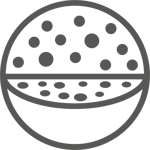
Liposomes, Nanoemulsions, Nanoencapsulation and More
The key to the Microfluidizer® technology's remarkable efficiency is the design of our exclusive fixed-geometry Interaction Chamber™. As fluids are forced at constant pressures and controlled temperatures through the unique Interaction Chamber™, materials experience extreme shear forces, yielding precisely controlled particle size reductions and strikingly tight particle size distribution curves.
The ability to control the level of shearing provides customers the flexibility to use less energy to achieve particle size reduction targets — which are often smaller than those possible using ordinary homogenizer technologies.
Needless to say, it’s one thing to develop an effective process during the research and development phase, while it is often another thing entirely to attempt to scale up that process to full production-run volume. By ensuring guaranteed scale-up success, Microfluidics provides customers the ability to sidestep this common potential pitfall.
Whether you use our carefully engineered machines to achieve cell disruption, nanoemulsions, nanoencapsulation, liposomes, or some other cutting-edge application, you can depend on Microfluidizer® technology to deliver the particle size reductions you require, more efficiently and more consistently, regardless of where you are in the development process for your droplet microfluidics applications.